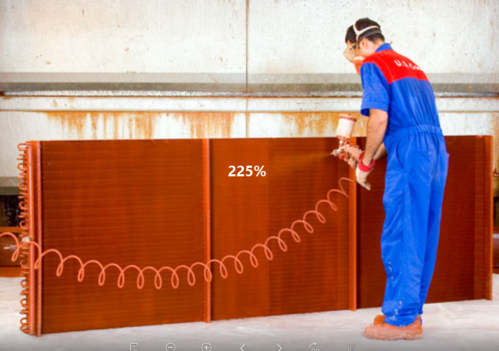
Our houses could have more than a few metal objects that can be subjected to slow process of corrosion. There are multiple protective coatings we could use, such as zinc chromate, zinc phosphate, zinc dust and red lead. In some cases, it is not possible to prevent corrosion and we could only minimize the rate of corrosion. In this case, corrosion will become relatively negligible that it won’t be visible to naked eyes. Corrosion prevention material should have very high electrical resistance, such as chlorinated rubber, vinyl, phenol and catalyzed epoxy. We may also use pigments to increase the resistance, such mica, china clay, talc and even rusted iron itself, the iron oxide. Before applying the anti corrosion material on the surface, we should remove all the dirt and grit that could actually accelerate the rate of corrosion.
Higher electrical resistance can be achieved with thicker coating. Coating should also limit exposure to salt, water and oxygen. In this case, the coating also works as a barrier to prevent the metal part to come into contact with corrosive materials. For this reason, we should choose coating that contains chlorinated rubber, vinyl, polyurethane, coal tar epoxies and catalyzed epoxy, because they have low permeability to water and more importantly, oxygen. On the other hand, oil-based coatings and alkyds are more permeable to corrosive material. That’s the reason why we need to properly clean the metal surface, because it is a bad idea to have traces of corrosive substances trapped under the coating. This will also ensure maximum adhesion between steel and coating. Coatings we choose should be conducive to the characteristics of the metal part.
Good coating should resist chemical exposures, high temperature, abrasion, oil and fire. There are different types of anti corrosion coatings and they should have higher performance in dealing with our situations. The decision of purchasing specific type and brand of the coating should depend on our budget. The coating should have longer duration in protecting the metal part. Coating should also be ideal for our decorative purposes. Some of them require air drying, while others may need hardener or catalyst, so they can be cured with chemical reactions. For best result, we should consult with the seller to make sure that the anti-corrosion coating can be used for our requirements. As an example, people who live near the sea, could need to different kind of coating, compared to people who stay at higher grounds.
Application can be performed using airless spray, conventional spray, roller and brush. In some cases, airless and air-based spray can’t be used for specific situations, so roller and brush could be more suitable. However, application using brush can be quite slow, but conventional spray could be applied on metal objects with ornate decorative shapes. However, the quickest method of application is probably the airless spray. These sprays can be used for many types of paint and we can determine the desirable thickness.